Enabling Innovation: A Manufacturing Veteran’s Guide to Staying Ahead (Or Relevant)
The latest round of U.S. tariffs on essential manufacturing components is leading investors to adjust their risk assessments to favor startups with resilient supply chains. In this guest commentary, John Haddox of Decision Resources explains how manufacturing startups and venture capitalists can navigate the changes.
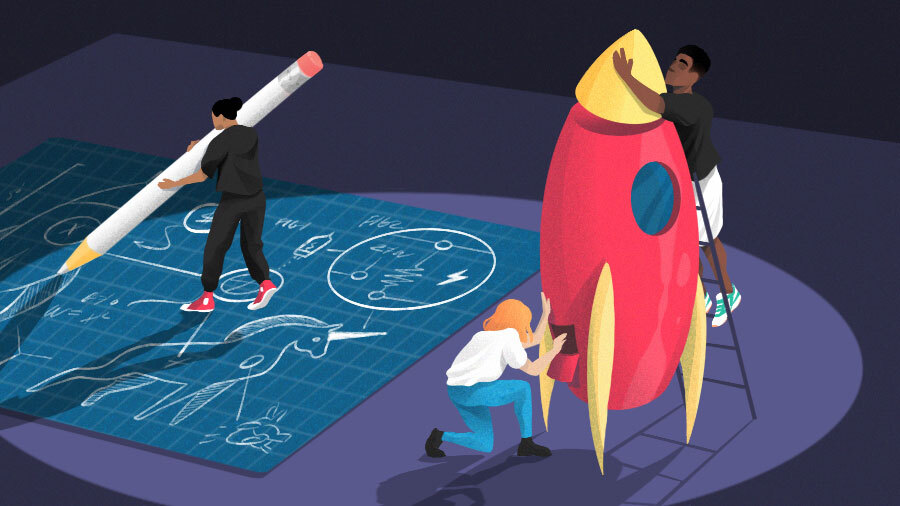
By John Haddox
Whether it’s the latest aircraft landing gears, hygienic air filters or smart-home devices, product designers are always on the hunt for new configurations that could become the “next big thing.”
Yet it’s manufacturing companies that turn these dreams into a reality — innovating production lines and processes to fulfill tasks in the most cost-effective way possible. This presents a golden opportunity for startups, entrepreneurs and investors looking to disrupt the manufacturing sector.
Do your homework
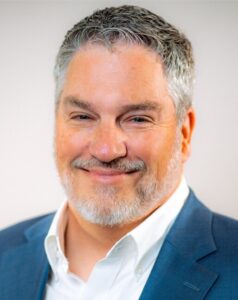
Although it’s tempting to get caught up in the whirlwind of consumer-driven innovation and jump in feet first, it’s crucial to balance that excitement with strategies for long-term stability.
The latest round of U.S. tariffs on essential manufacturing components is forcing companies to rethink their sourcing strategies, production costs and pricing models. For startups in the space, these changes can be especially difficult to absorb, as they often lack the purchasing power and supplier networks of established manufacturers.
Investors, too, are adjusting their risk assessments — favoring startups with resilient supply chains and flexible cost structures over those reliant on fragile global dependencies.
While government initiatives such as the MBDA‘s Advanced Manufacturing Centers support the manufacturing industry, these opportunities are limited and funding can be hard to come by.
Let’s examine how manufacturing startups and venture capitalists can navigate these changes and take innovation into their own hands.
Create a step-by-step plan
To enable innovation, it’s important not to run before you can walk.
Manufacturing startups must have a clear path to profitability that includes financial projections, market analysis and scenario planning. Understanding the technology trends, embracing lean methodologies and speaking with industry veterans will help turn pipe dreams into production lines.
Recognizing the financial constraints and scalability needs of startups, consider a modular approach to building facilities and implementing technologies. This is not only more affordable but also more manageable, reducing the failure risk. Infrastructure as a service, platform as a service, and software as a service give manufacturers the flexibility to build out projects step by step and scale to new sites or functions as and when they are ready.
IaaS, PaaS, and SaaS help reduce upfront capital expenditures by hosting innovative technology, such as predictive maintenance, in secure cloud environments. Manufacturing startups can pay for the computing resources they use and avoid investing heavily in servers, storage and software licenses. This helps when starting out, when the budget is low.
Having a trusted technology partner also reduces overhead costs and specialized skills training.
Ensure interoperability
A significant shift is expected in the manufacturing sector within the next two years.
Manufacturing processes are already complex, involving many constituent apps and inputs that need to work together. The expected rapid adoption of integrated platforms — rising from under 40% in 2023 to 70% by 2026 — will add a further layer of complexity, which means interoperability needs close management from day one.
Here’s how standardized data models help.
Most manufacturing companies already have fairly intricate digital ecosystems that typically include ERPs, databases, PLCs, SCADA systems, CAD software, sensors and PLM systems. Standardized data models are essential to effectively handle massive datasets and guarantee seamless communication between products, assets and applications.
The good part is startups can ensure this from the get-go with cloud ERP built for manufacturing.
When data is structured and organized according to common standards, it becomes much easier to share and integrate information from different sources. Manufacturers can then leverage advanced analytics tools to gain valuable insights into their operations, customer needs and market trends, helping them become more agile and empowering them to stay ahead of the curve.
Stay relevant
Widely recognized industry standards to put on your radar (if they aren’t already) include ISO, ANSI and IEC. Following these helps ensure interoperability and data exchange with partners and customers.
Building a manufacturing firm is capital-intensive and complex. However, breaking down large-scale innovation efforts into smaller, modular projects offers a more manageable and cost-effective approach.
By standardizing data protocols and integrating new platforms step by step, teams can focus on specific areas for improvement, reducing both the financial burden and the risk of disruption. Manufacturing startups adopting this modular approach invite gradual and continuous improvement, reducing risk for investors and making innovation more attainable and sustainable.
John Haddox is the COO of Decision Resources Inc. He has a strong and diverse background in manufacturing, operations, CRM and IT project management. Prior to joining DRI, he held positions in operations management and logistics management at Thermal Industries and Bayer Corp.
Illustration: Dom Guzman