Inside the climate innovations reshaping our buildings
The Fast Company Impact Council is an invitation-only membership community of leaders, experts, executives, and entrepreneurs who share their insights with our audience. Members pay annual dues for access to peer learning, thought leadership opportunities, events and more. Across industries, a new era of climate innovation is accelerating. The momentum is visible in the data: Global clean energy investment surpassed $2 trillion for the first time in 2024, double the amount invested in fossil fuels. While solar panels, wind turbines, and grid-connected batteries often grab the headlines, the low carbon economy is growing in far more corners than many realize. Since founding Supercool last summer to cover proven and scaling climate solutions, I’ve seen needle-moving innovation accelerating across farms, factories, and finance departments. One sector in particular shows remarkable progress—the built environment, which accounts for 34% of global carbon emissions. From hard tech and material breakthroughs to AI-powered intelligence to novel business models, here are three approaches to decarbonizing buildings happening now. 1. Hardtech innovation: Build with carbon-negative materials The engineered materials we use to build our suburbs and cities—primarily timber, concrete, and steel—create a lot of carbon emissions in their manufacture. Concrete and steel account for nearly 18% of global greenhouse gas emissions. Wood-based materials like oriented strand board (OSB), which are commonly installed in new homes, generate most of their manufacturing carbon emissions from burning wood to generate heat during production. Plantd transforms the built environment using carbon-negative building materials derived from alternative biomass—a hardy, fast-growing grass. Four years ago, I cofounded the company with two former SpaceX engineers. To realize its ambitions, Plantd established a new agricultural supply chain innovating at every step, from building an in-house tissue culture lab to establishing full-scale greenhouse operations to supplying commercial farmers with the company’s proprietary grass. [Photo: Courtesy of Plantd] Why grass? Because it grows incredibly fast, like bamboo, rapidly removing atmospheric carbon in the process, and possesses the structural characteristics to be transformed into durable engineered building materials. Yet, the key to sequestering carbon in our materials is Plantd’s manufacturing technology. Our team pioneered a modular, electric-powered production line that turns grass into finished products that replace plywood and OSB in new home construction. It’s a first-of-its-kind technology that distinguishes a Plantd production facility from every other engineered wood facility in the world; ours is the only one without a smoke stack on top of the building. This past fall, D.R. Horton, the largest homebuilder in America, which builds about one in every 10 U.S. homes, ordered 10 million Plantd panels, enough to form the walls and roofs of 90,000 new single-family homes. 2. Software innovation: Give buildings brains An even bigger source of building-related carbon emissions is the energy required to operate them. Globally, this accounts for 26% of all greenhouse gas emissions. The top culprit: HVAC systems. The heating, cooling, and ventilation equipment needed to keep us comfortable indoors are responsible for about 35% of all energy used in U.S. buildings. The challenge is that thermostats, even the smart ones, aren’t very bright. They can track what’s already happened and react to what’s happening right now, but they cannot anticipate changes in weather, occupancy, carbon intensity of the grid, and energy costs. BrainBox AI can. Using AI-powered intelligence, its cloud-based control system connects to the hundreds, sometimes thousands, of HVAC components in a building and sends them real-time instructions. The company’s platform provides over 15,000 buildings worldwide—from Nordstrom to Family Dollar—with the intelligence to see six hours into the future with 96% accuracy. By knowing the future, BrainBox AI cuts energy, costs, and carbon emissions and improves comfort. It’s an easy-to-install solution that works with existing systems and equipment. The results? HVAC-related emissions reductions of up to 40% and energy savings as high as 25%. 3. Finance innovation: Make efficiency upgrades free Many buildings are stuck with legacy equipment that gets the job done but consumes far more energy than their more efficient modern counterparts. Yet, new equipment can cost hundreds of thousands of dollars, often placing upgrades out of reach. Budderfly has built one of the fastest-growing businesses in America by removing the cost barrier. The company identifies energy-intensive businesses like fast food chains and offers them a deal that sounds almost too good to be true: free upgrades to en
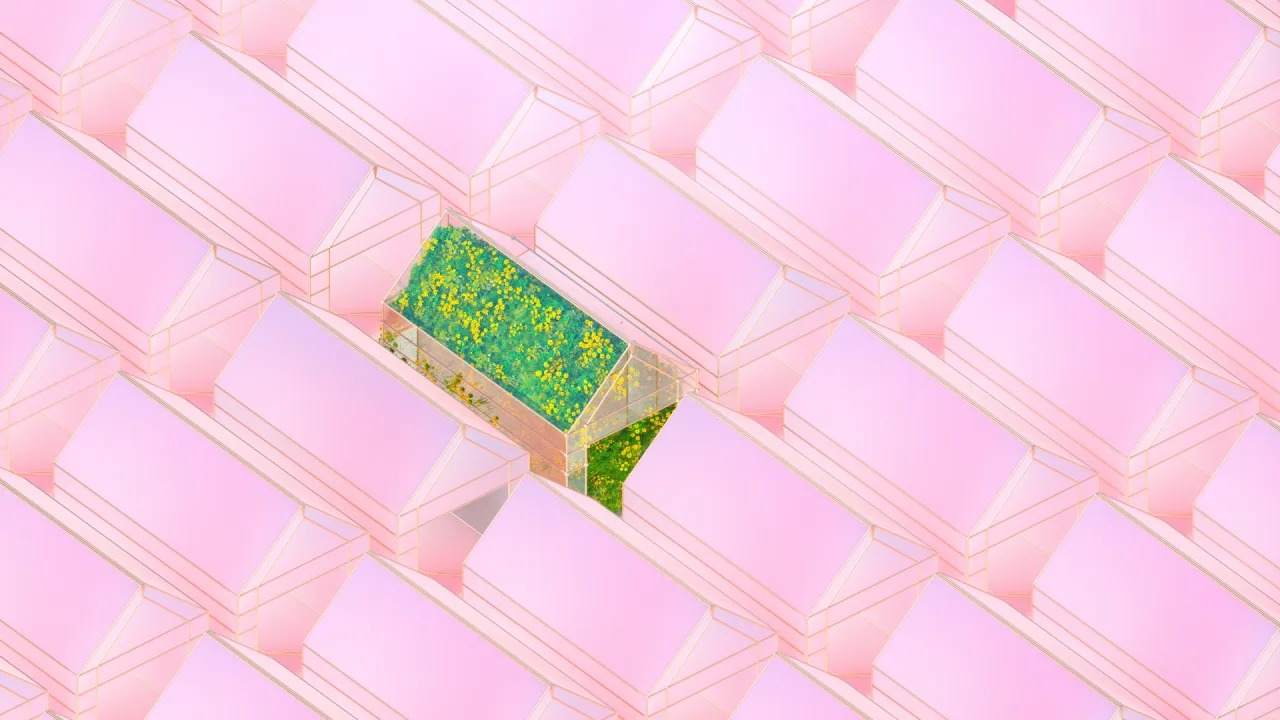
The Fast Company Impact Council is an invitation-only membership community of leaders, experts, executives, and entrepreneurs who share their insights with our audience. Members pay annual dues for access to peer learning, thought leadership opportunities, events and more.
Across industries, a new era of climate innovation is accelerating. The momentum is visible in the data: Global clean energy investment surpassed $2 trillion for the first time in 2024, double the amount invested in fossil fuels.
While solar panels, wind turbines, and grid-connected batteries often grab the headlines, the low carbon economy is growing in far more corners than many realize.
Since founding Supercool last summer to cover proven and scaling climate solutions, I’ve seen needle-moving innovation accelerating across farms, factories, and finance departments.
One sector in particular shows remarkable progress—the built environment, which accounts for 34% of global carbon emissions.
From hard tech and material breakthroughs to AI-powered intelligence to novel business models, here are three approaches to decarbonizing buildings happening now.
1. Hardtech innovation: Build with carbon-negative materials
The engineered materials we use to build our suburbs and cities—primarily timber, concrete, and steel—create a lot of carbon emissions in their manufacture. Concrete and steel account for nearly 18% of global greenhouse gas emissions. Wood-based materials like oriented strand board (OSB), which are commonly installed in new homes, generate most of their manufacturing carbon emissions from burning wood to generate heat during production.
Plantd transforms the built environment using carbon-negative building materials derived from alternative biomass—a hardy, fast-growing grass. Four years ago, I cofounded the company with two former SpaceX engineers. To realize its ambitions, Plantd established a new agricultural supply chain innovating at every step, from building an in-house tissue culture lab to establishing full-scale greenhouse operations to supplying commercial farmers with the company’s proprietary grass.
Why grass? Because it grows incredibly fast, like bamboo, rapidly removing atmospheric carbon in the process, and possesses the structural characteristics to be transformed into durable engineered building materials.
Yet, the key to sequestering carbon in our materials is Plantd’s manufacturing technology. Our team pioneered a modular, electric-powered production line that turns grass into finished products that replace plywood and OSB in new home construction.
It’s a first-of-its-kind technology that distinguishes a Plantd production facility from every other engineered wood facility in the world; ours is the only one without a smoke stack on top of the building.
This past fall, D.R. Horton, the largest homebuilder in America, which builds about one in every 10 U.S. homes, ordered 10 million Plantd panels, enough to form the walls and roofs of 90,000 new single-family homes.
2. Software innovation: Give buildings brains
An even bigger source of building-related carbon emissions is the energy required to operate them. Globally, this accounts for 26% of all greenhouse gas emissions.
The top culprit: HVAC systems.
The heating, cooling, and ventilation equipment needed to keep us comfortable indoors are responsible for about 35% of all energy used in U.S. buildings.
The challenge is that thermostats, even the smart ones, aren’t very bright. They can track what’s already happened and react to what’s happening right now, but they cannot anticipate changes in weather, occupancy, carbon intensity of the grid, and energy costs.
BrainBox AI can. Using AI-powered intelligence, its cloud-based control system connects to the hundreds, sometimes thousands, of HVAC components in a building and sends them real-time instructions.
The company’s platform provides over 15,000 buildings worldwide—from Nordstrom to Family Dollar—with the intelligence to see six hours into the future with 96% accuracy.
By knowing the future, BrainBox AI cuts energy, costs, and carbon emissions and improves comfort. It’s an easy-to-install solution that works with existing systems and equipment.
The results? HVAC-related emissions reductions of up to 40% and energy savings as high as 25%.
3. Finance innovation: Make efficiency upgrades free
Many buildings are stuck with legacy equipment that gets the job done but consumes far more energy than their more efficient modern counterparts. Yet, new equipment can cost hundreds of thousands of dollars, often placing upgrades out of reach.
Budderfly has built one of the fastest-growing businesses in America by removing the cost barrier. The company identifies energy-intensive businesses like fast food chains and offers them a deal that sounds almost too good to be true: free upgrades to energy-efficient systems, including HVAC, lighting, refrigeration, and security. Budderfly foots the bills and shares the monthly energy savings with its customers.
Scale is key to making this business model work. Budderfly has raised nearly $1 billion to pay for the equipment it installs in customer locations. Its rapid expansion enables it to secure preferential pricing from global equipment suppliers that individual owners and franchisees could never obtain independently.
Budderfly also takes over billing, which is one less thing for customers to worry about, and gives the company a trove of data to drive further energy reductions and cost savings.
From Taco Bell to McDonald’s to Sonic, clients are guaranteed to see savings from day one. In 2024, Budderfly generated $200 million in revenue and now operates in more than 7,000 locations nationwide. Its customers’ collective energy use dropped 43% last year.
The takeaway
Whether it’s growing new materials, giving buildings the ability to think ahead, or reimagining who pays for energy systems, the low carbon economy isn’t just coming someday. It’s already being built.
Josh Dorfman is the CEO and host of Supercool.