How battery recycling can solve India’s EV waste crisis before it begins
Learning from global examples, India can set up a recycling infrastructure that supports a circular economy for battery materials like copper, nickel, and aluminium. With the right policies, public awareness, and investments in low-carbon technologies, India can set a global example.
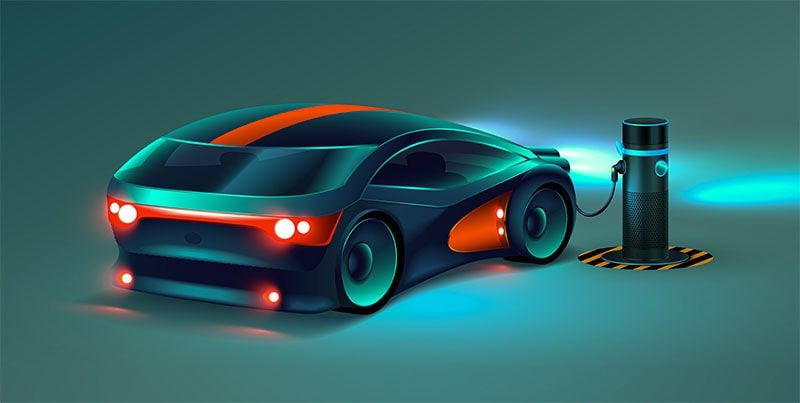
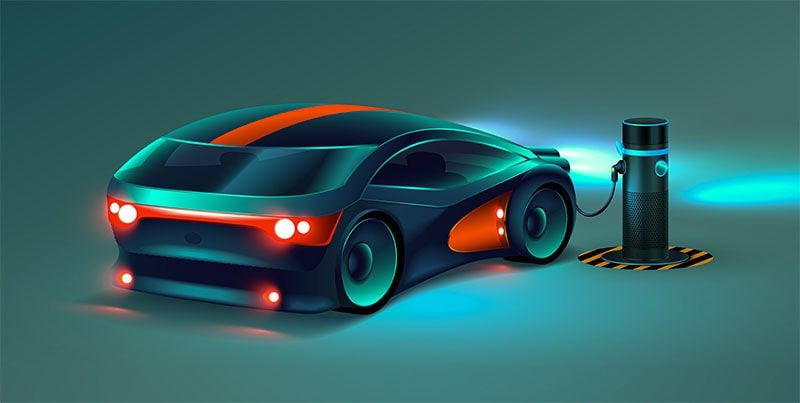
In India, we are at the brink of an electric vehicle (EV) revolution. The government is pushing a target of 30% EV adoption by 2030, and automakers are introducing electric models—all actions aimed at creating an electric future. This future comes with a hidden challenge: battery waste. EV batteries (lithium-ion primarily), which are at the heart of EVs, have a lifespan of 8-10 years. After their lifespan is depleted, they become a ticking environmental time bomb without a waste disposal and contingency plan.
In 2024, EVs accounted for approximately 7.4% of all vehicles sold in India, up from 6.38% in 2023, according to the data from the Vahan portal cited in the Society of Manufacturers of Electric Vehicles. India is expected to generate over 500,000 metric tons of used lithium-ion batteries ready for recycling by 2030, noted a report by the Confederation of Indian Industry. These bulky batteries will overfill landfills, be a fire hazard, and leak chemicals like cobalt, nickel and lithium into soil and water, causing environmental damage, and their valuable contents will be lost for use if we do not have a plan to manage this waste.
The question is: now that we can foretell the problem and its magnitude, can we prevent it? Could we perhaps have an opportunity in the wake of preventing the crisis? If India could build a circular economy for battery materials, ensuring no dead battery ends up in landfills and instead is mined for its contents remade into new batteries or other goods, we have a solution and an opportunity at hand. This is where battery recycling comes in—a solution that we must adopt before the waste crisis begins. (Representative image)
Learning from EV blueprints
China, the world’s largest EV market, faced the same scenario a decade ago. By 2020, China was producing over 240 metric kilotons of waste EV batteries yearly (Ellen McArthur Foundation) and it effectively managed to turn the waste problem into an opportunity and built a robust battery recycling system. With the combination of government policies and innovation in recycling, by 2021, China had a recycling capacity of nearly 188 metric kilotons of used lithium-ion batteries, according to a Canary Media report.
On the other hand, other countries with mature EV markets are grappling with the economic and logistical challenges of recycling. In the US, battery recycling is not economically viable on a large scale yet, as collection, transportation and processing costs often outweigh the value of recovered materials.
All of these global insights contain valuable lessons for India. The success of the EU (current capacity estimate: 300,000 metric tons) and China’s regulatory support can be mimicked, and the US’ scale and logistical challenges can be avoided in India, but we also have to consider our unique context. India has a growing demand for metals and a nascent EV market, making it possible to build an efficient recycling ecosystem.
The Indian scenario
Since the EV market is still nascent, India’s EV battery manufacturing is still in its early stages. Hence, we do not need a circular economy for batteries as there is no established battery manufacturing or CAM/pCAM (precursor cathode active material) manufacturing (required for manufacturing battery cathode material). However, EV recycling is a must to effectively prevent EV battery waste buildup and provide valuable materials, with a lower carbon footprint.
Copper, aluminium, nickel and plastics (which are contained in batteries) are widely used across industries such as construction, electrical, automotive, etc—all extremely important industries in a growing economy like ours. What we need is a circular economy for metals and plastics. Almost 38% of India’s copper demand is met from scrap, according to the Indian Bureau of Mines. India has a huge demand for aluminium and nickel scrap as well. The coming battery waste volumes can easily be harnessed for this demand.
For recycling to avoid the pitfalls faced by the US of high collection, logistics and processing costs, the technologies used need to be efficient in recovery rates, and the value of recovered materials must recover operational costs. Collection and pre-processing can be decentralised for better streamlining of operations. We already have an advantage as India can support large-scale operations and keep labour costs low. China also has a problem of a shadow economy of unregistered recyclers, with many of the recyclers not being registered and operating without following government norms and environmental and safety regulations. With a strong regulatory framework, India can avoid the same.
The way forward
Our policy frameworks need to be strong, to incentivise recycling. Public awareness is also critical. Battery Waste Management rules, 2022 are a step in the right direction by the government but more needs to be done.
India’s EV journey is just beginning, and we can set a global example in sustainability. By investing in the development of low carbon recycling technologies and focusing on the circular economy of metals we can address the future challenge of battery waste before it becomes a crisis. By creating value from waste, instead of just managing waste, we can ensure that India’s EV revolution is not only green but also sustainable for generations to come.
(Shubham Vishvakarma is the Founder and Chief of Process Engineering at Metastable Materials Private Limited.)
Edited by Kanishk Singh
(Disclaimer: The views and opinions expressed in this article are those of the author and do not necessarily reflect the views of YourStory.)